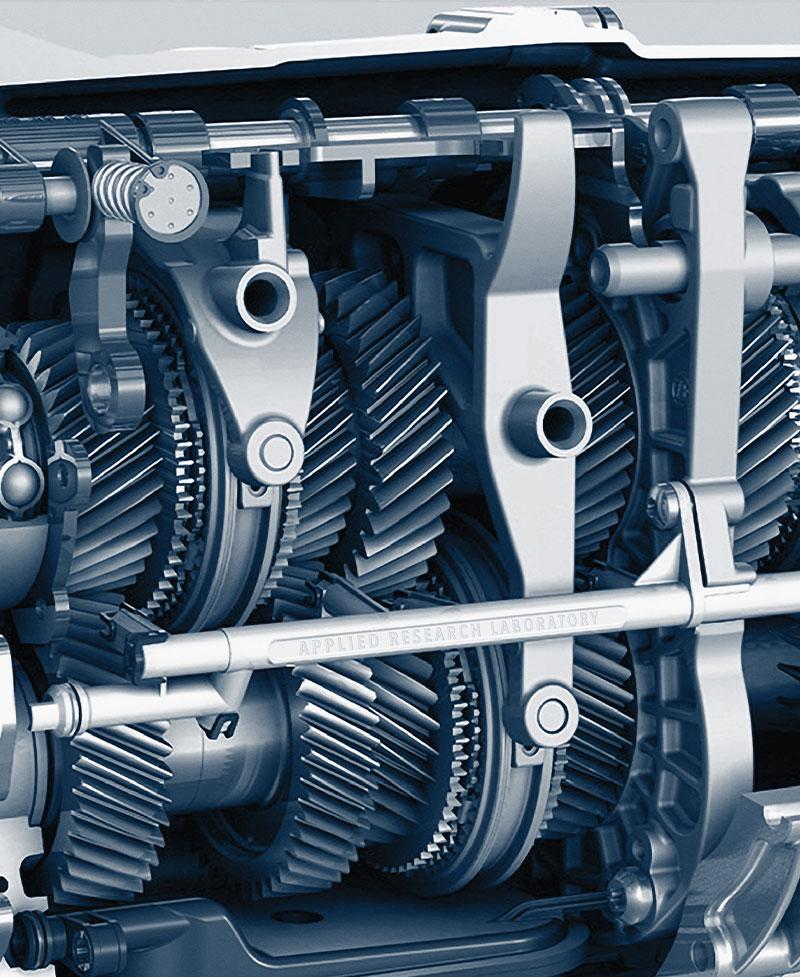
The DTC came into being in 1992 under the auspices of the U.S. Navy MANTECH program. It is currently sponsored by various federal agencies and the gear and transmission manufacturing industry (aerospace, automotive and marine) in the United States and abroad. R&D services to the gear/drivetrain industry include gear manufacturing/process support, performance testing and characterization of all things gear related, including metrology, metallurgy, failure analysis, prognostics, etc. The DTC also operates the AGMA, ASME Gear Research Institute, under a multi-year contract.
The primary objectives of the R&D efforts at the DTC are to increase performance and reduce costs of mechanical power transmission systems and components. There are several metrics of performance. They include higher power density, increased component durability, and reduced operational vibration and noise. To fulfill these objectives, a variety of sponsored projects focusing on manufacturing, materials, and metrology have been undertaken or are ongoing at the DTC.
In the area of manufacturing, we spend a considerable amount of effort characterizing the impact of current processes on the durability of transmission components such as gears, while focusing efforts in developing novel manufacturing processes for the same. Characterizing the durability of various advanced steels for gear applications and optimizing their performance is a major component of the DTC’s efforts in the area of materials.
The DTC is very well equipped with the necessary hardware to conduct R&D efforts in these areas. A battery of rolling/sliding contact fatigue testers, tooth bending test facilities, and low speed and high speed re-circulating gear testers are available. A gear metrology facility equipped with an M&M CNC gear inspection machine, a MAAG gear checker and a ZEISS coordinate measuring machine (CMM) are also available at the DTC. Also resident at the DTC is the world’s first production capable, double-die gear ausform finishing machine (discussed below).